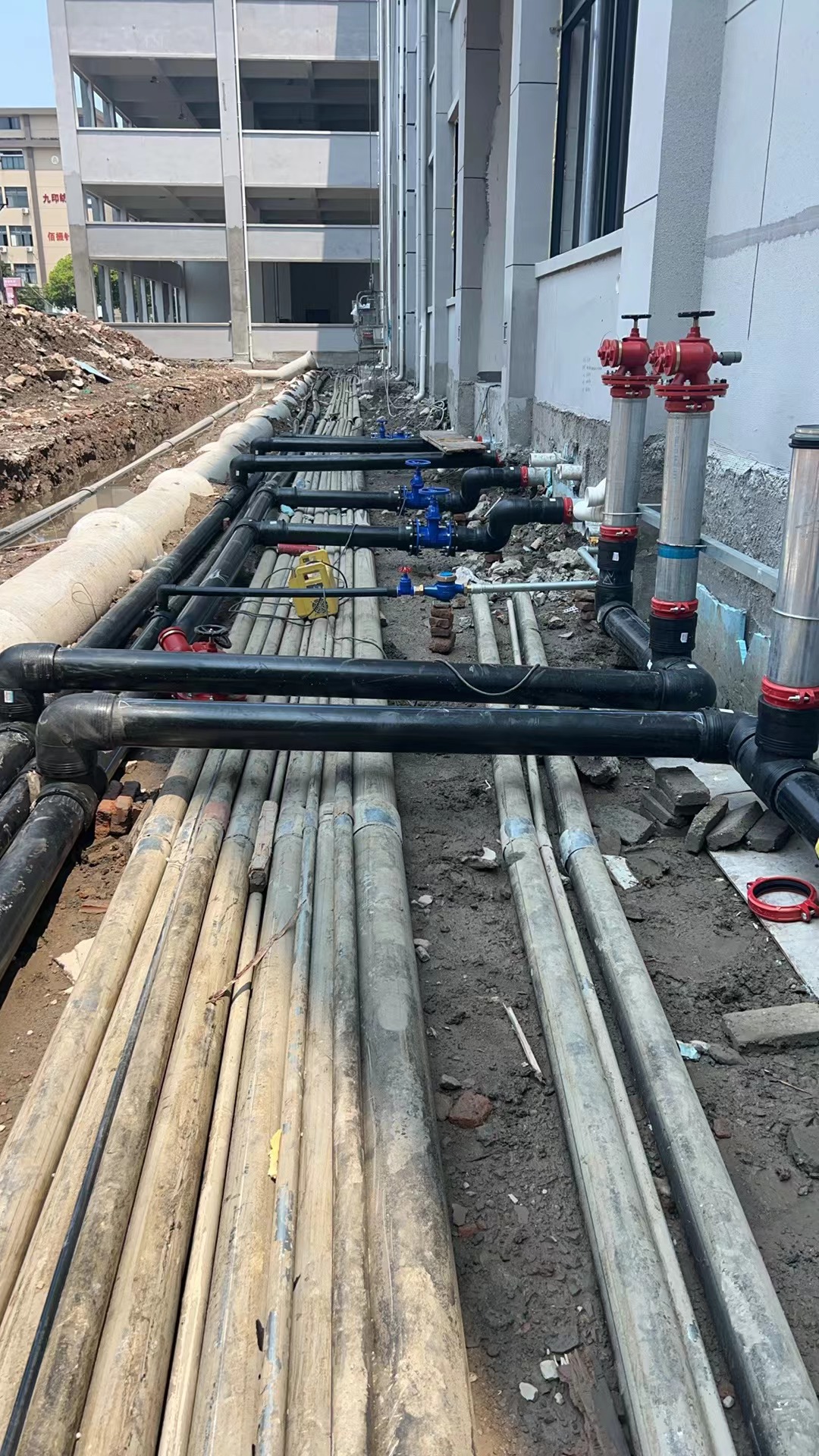
When it comes to adjusting the welding parameters of a Hdpe pipe Butt Welding Machine based on the pipe fitting materials, several key steps need to be followed:
- Understand the Material Properties:
- Different materials have distinct melting points, thermal conductivities, and chemical stabilities. For instance, polyethylene (PE) has a relatively low melting point, while polypropylene (PP) has a higher one.
- Determine the Welding Temperature:
- Refer to the technical data of the pipe fitting materials to obtain the recommended welding temperature range.
- Commonly, for PE pipe fittings, the welding temperature usually ranges from 200 to 230 degrees Celsius. For PP pipe fittings, it might be around 250 to 280 degrees Celsius.
- Adjust the Heating Time:
- The thermal conductivity of the material influences the heating time. Materials with low thermal conductivity require longer heating time to achieve a uniform temperature distribution.
- Thicker pipe fittings also need more heating time.
- Set the Welding Pressure:
- The hardness and strength of the material affect the required welding pressure. Harder and stronger materials might need higher pressure for a good welding bond.
- Usually, the adjustment of pressure needs to be determined based on practical tests and experience.
- Control the Cooling Time:
- Different materials have different requirements for the cooling speed. Some materials need slower cooling to reduce internal stress, while others can cool faster.
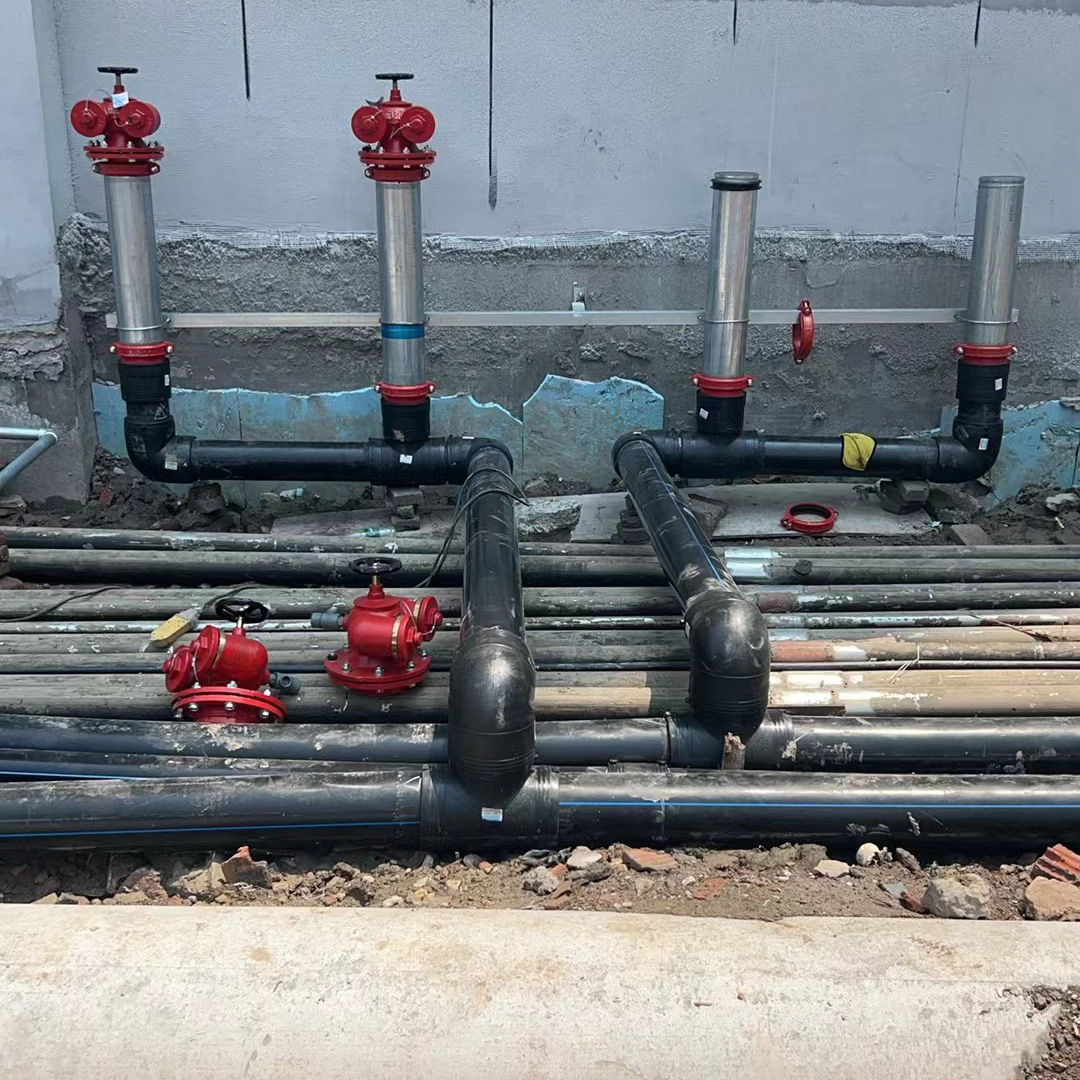
In conclusion, adjusting the welding parameters of a hot melt butt welding machine based on the pipe fitting materials requires a comprehensive consideration of factors such as material properties, size, and shape. Through tests and practical operations, the parameters can be continuously optimized to ensure high-quality welding joints.