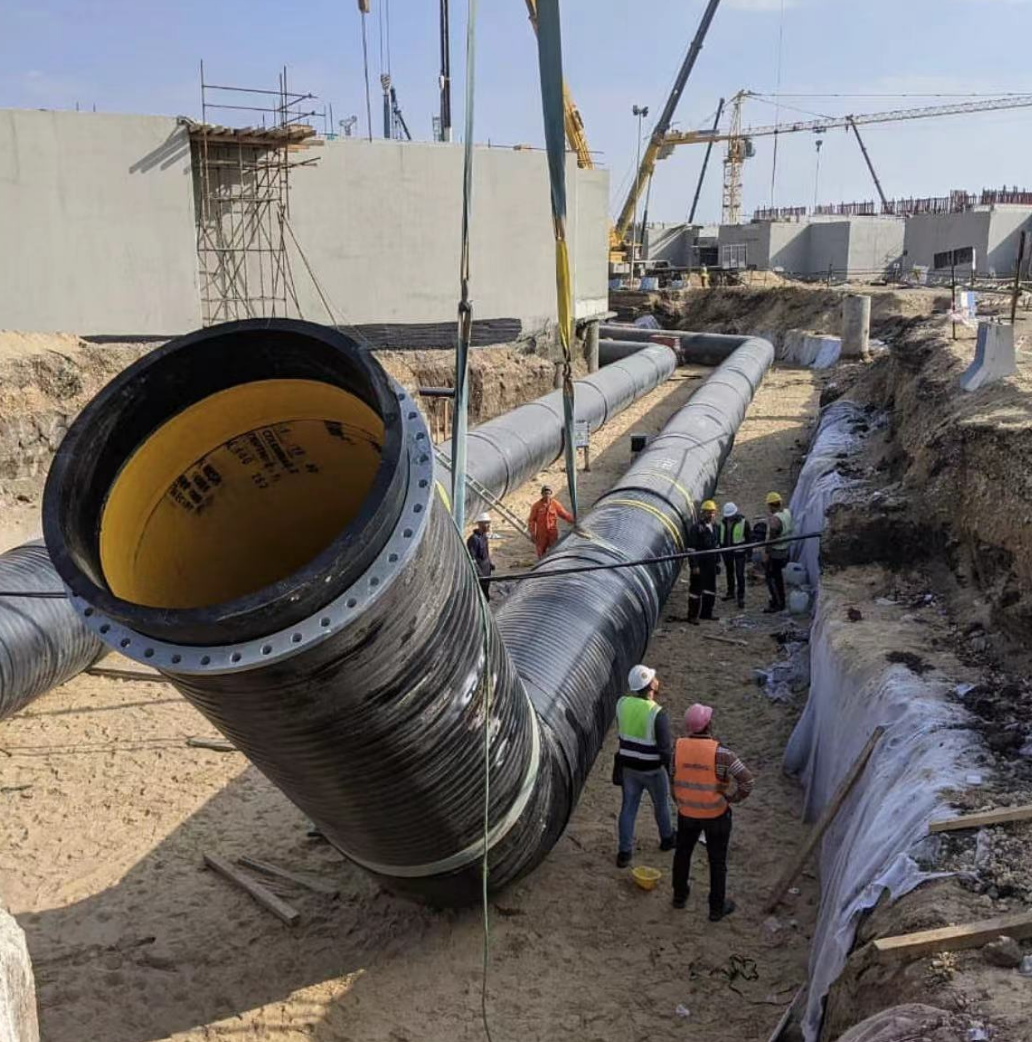
Butt fusion welding machines are essential tools in the welding of thermoplastic pipes. These machines operate by heating the ends of two pipes simultaneously until they reach a molten state. The pipes are then pressed together under pressure, resulting in a fusion of the material that creates a strong, homogenous joint. The choice of materials that can be welded using butt fusion machines is limited to thermoplastics, which have the necessary properties to undergo this heating and fusing process. This article will explore the different types of materials that are compatible with butt fusion machines and discuss their common applications.
1. Polyethylene (PE) Polyethylene is the most widely used material for butt fusion welding machine. This material is favored for its versatility, durability, and cost-effectiveness. Polyethylene pipes come in different grades, such as:
- High-Density Polyethylene (HDPE): HDPE is known for its high strength-to-density ratio, making it suitable for water, gas, and sewage pipelines.
- Medium-Density Polyethylene (MDPE): MDPE offers a good balance between flexibility and strength, often used in gas distribution networks.
- Low-Density Polyethylene (LDPE): LDPE is more flexible and is often used in applications requiring lighter-duty piping.
2. Polypropylene (PP) Polypropylene is another material frequently used with hot-melt butt fusion machines. It is recognized for its chemical resistance and thermal stability. The main types of polypropylene used in pipe welding include:
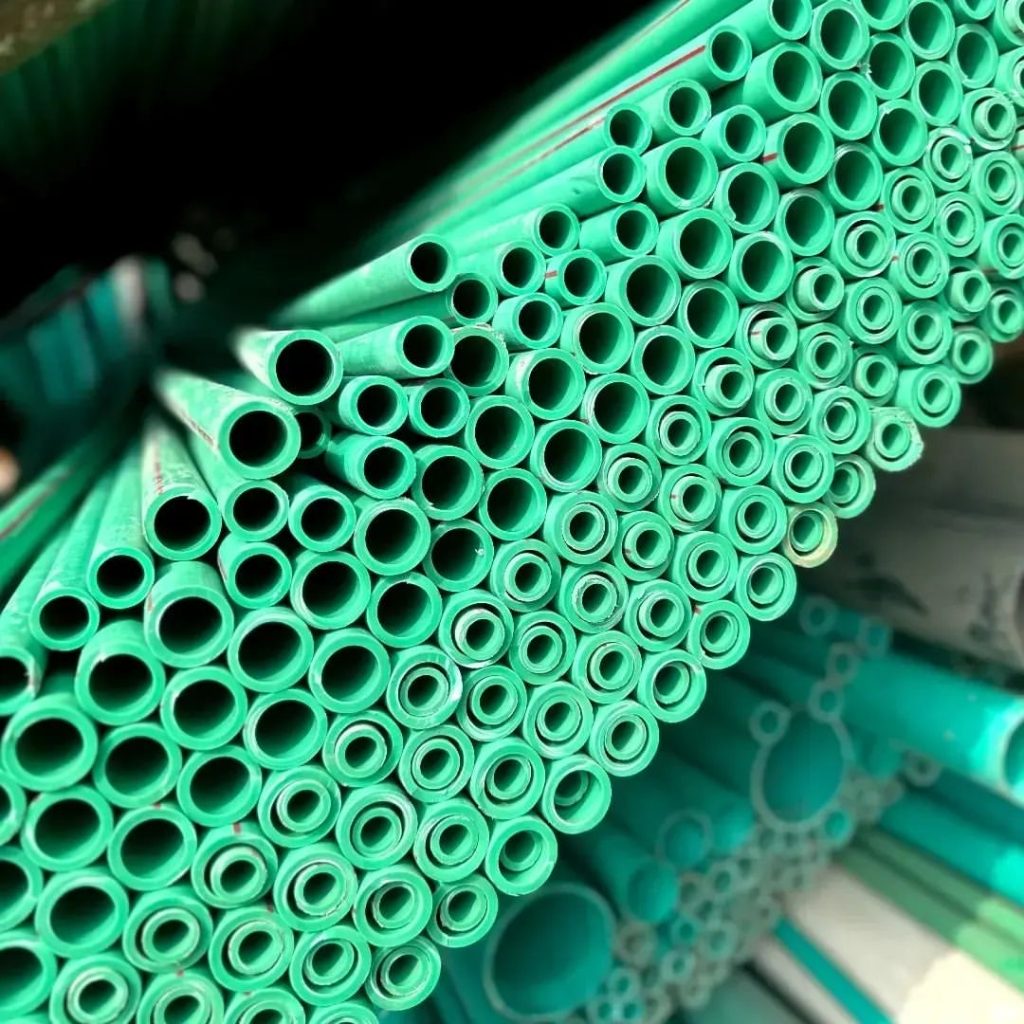
- Homopolymer Polypropylene (PP-H): Used in industrial applications due to its high chemical resistance and mechanical strength.
- Block Copolymer Polypropylene (PP-B): This material is more impact-resistant and is typically used in infrastructure applications, such as sewer systems.
- Random Copolymer Polypropylene (PP-R): PP-R is commonly used in plumbing and heating systems because of its pressure resistance and durability.
3. Polybutene (PB) Polybutene, also known as polybutylene, is mainly used in the plumbing and heating sectors. Its flexibility and resistance to scaling make it an excellent choice for hot water and underfloor heating systems. Polybutene pipes can be reliably welded using hot-melt butt fusion techniques, ensuring leak-proof joints in systems where water quality and temperature consistency are critical.
4. Polyvinyl Chloride (PVC) Polyvinyl chloride is another thermoplastic material that can be welded with hot-melt butt fusion machines, though it is less common compared to the others. PVC is often used in drainage, ventilation, and electrical conduit systems. The chlorinated version of PVC, known as CPVC (Chlorinated Polyvinyl Chloride), is more suitable for hot-melt butt fusion due to its higher heat resistance, making it ideal for hot water systems and industrial liquid handling.
5. Polyvinylidene Fluoride (PVDF) Polyvinylidene fluoride is a high-performance thermoplastic known for its outstanding chemical resistance and high-temperature tolerance. PVDF pipes are typically used in the chemical processing, semiconductor, and pharmaceutical industries. Hot-melt butt fusion is a preferred welding method for PVDF due to the material’s ability to form robust and reliable joints, even under harsh environmental conditions.
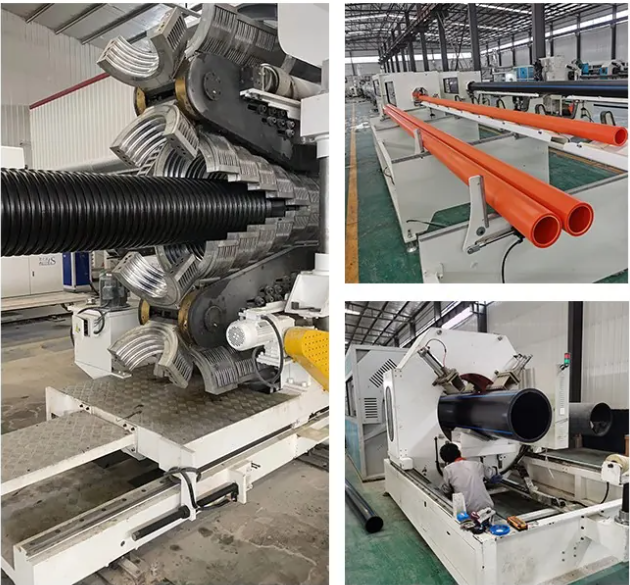
Butt fusion welding machine are indispensable for creating strong and durable joints in thermoplastic pipes. The key materials compatible with these machines include polyethylene (PE), polypropylene (PP), polybutene (PB), polyvinyl chloride (PVC), and polyvinylidene fluoride (PVDF). Each of these materials has unique properties that make them suitable for specific applications, from water distribution and gas pipelines to chemical processing and high-temperature systems. Understanding the compatibility and characteristics of these materials is crucial for achieving optimal results in thermoplastic pipe welding projects.